How a 3D printer works
An ongoing debate over legalizing 3D printed guns is bringing the technology to a new audience.
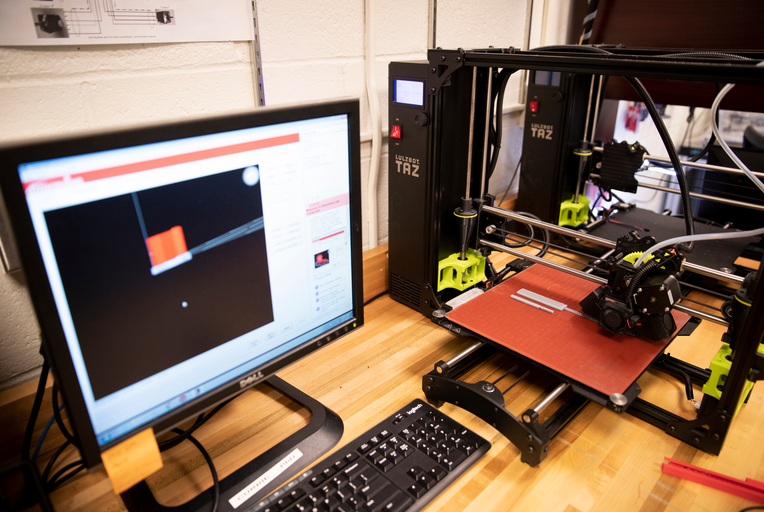
In 2018, printing a document or photo is as simple as hitting a button and the finished product arrives in seconds. But what happens when you add an extra dimension?
Over the last several years, 3D printing has exploded and you’ll find specialized machines at libraries, universities or even your local office supply store. Still, 3D printers haven’t matched the ubiquity of their 2D cousins and an ongoing debate over legalizing 3D printed guns is bringing the technology to a new audience.
Additive manufacturing — 3D printing by another name — was invented in the 1980s and today, there are a variety of different methods and classes of printers. With the right machinery, you can build an object with just about any material, from ceramic to copper to resin, though plastic is the most common, especially at the consumer level.
At the most basic level, it’s similar to regular printing, just imagine the machine pouring plastic in vertical layers instead of ink in horizontal lines.
“The whole idea of additive manufacturing is that you put things down a layer at a time,” said Edward Currie, associate professor of engineering at Hofstra University. “When you build a house, you put down the foundation and then you start putting up the bricks and the walls.”
Making a 3D model
Unlike a traditional 2D printer, 3D printers require special files known as blueprints that specify the dimensions for a 3D object.
A process called “slicing” follows the blueprint and divides 3D drawings into the layers that the printer will trace out.
“The technical knowledge side of it is coming up with the drawings. That’s where the real work is,” Currie said. “It’s like when you print a word document, you just hit print. What’s the hard part? It’s creating the document, same thing.”
There are three ways to get a computer assisted design file.
You can draw the object yourself, using CAD software to create a 3D digital model, or you can use someone else’s blueprints. You can also replicate an existing item by using a laser and scanning software to create a blueprint.
Waiting for results
To create the object, you just hit print. It’s as simple as it sounds. The rest of the work is for the printer to do, Currie said.
The printer works like an oversized glue gun, eating up spools of plastic filament.
“We start with material that’s pretty thick, and you pass it through a heated nozzle and you force it to come out,” Currie said. “Out the other side comes something thinner than a human hair.”
The printer’s computer sees the object as a series of points on a plane, according to Makerbot, one of the leading manufacturers of 3D printers.
The printer’s nozzle moves between these points, depositing plastic on a printer tray along the way.
The time required for printing depends on what the user is creating. A night vision goggle frame Currie designed took 56 hours.
The time required will depend on the size of the object, the desired quality of the finish and how solid it is — tighter infill patterns take longer than loose ones, a smoother finish takes longer than a rough one.
All done
The final result may be a solid object or parts that need to be put together.
The quality of printers varies significantly, which is an important consideration, Currie said.
3D printers are available for as little as a few hundred dollars and as much as hundreds of thousands. If exact dimensions are important to you — such as if you’re printing several objects that need to fit together like a puzzle — you’ll need a machine that’s much more expensive. Cheaper printers also can’t produce as smooth of a finish.
On Thursday, printers in Currie’s lab hummed for several hours, slowly building the latest version of wound closure clips. Once finished, magnets are attached.
The clips can be attached to either side of an open wound and the magnets will hold the wound together. A whole set can be used to close a wound more precisely than traditional stitches.
And if anything is not quite right with the clip, Currie just starts over. Traditionally, he’d have to request a new piece from the machine shop, which could take days or weeks. That’s the beauty of 3D printing, he said.
Deciding what to print
It’s a useful tool for creating prototypes and building models, Currie said. Jay Leno famously uses a 3D printer to replicate unavailable parts for restored cars so the parts can be custom manufactured.
In Currie’s lab, they’ve created dozens if not hundreds of versions of magnetic clips that can be used to help close open wounds, and other objects.
But uses are limited. Not every item is suited to be made from plastic — it’s fine for a robotic arm gear or a toy, but not practical for items that need to withstand high pressure or temperature. For example, experts said 3D printed plastic guns — which prosecutors say are illegal in New York state — are only durable enough for one or a few shots depending on the model, before they fall apart.
Read more about 3D printed guns here.